General Performance Curves
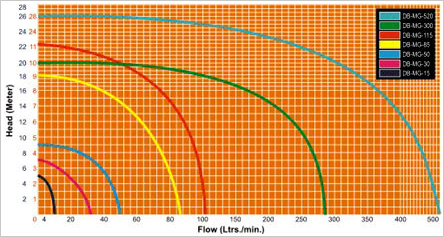
Advanced Magnetic Technology
LState-of-the-art magnetic technology provides a safe and reliable pump for difficult applications. A magnetic coupling consists of two magnet assemblies. One is the outer assembly (the drive magnet) and other is the inner assembly (the driven magnet). The outer assembly is connected to a motor and the inner assembly is directly attached to a pump impeller. When load is applied, the coupling effects angularly and magnets create a force which is used to transfer torque from the motor to the impeller. This permanent magnet coupling creates neither slippage nor induction current during rotation. There is no energy loss in this permanent - permanent magnet coupling. 'Daybreak' pumps have an inner magnet assembly which is directly molded into the impeller.
Engineered For Environment Safety
Daybreak offers magnetic drive chemical pumps which safety handle hazardous, highly corrosive, explosive and toxic chemicals. They provide safe, leak proof service because the magnetic coupling eliminates the need for traditional sealing methods, such as mechanical seals or gland packing. Which is the main source of leakage problems on pumps. As a result, down time and maintenance cost are greatly reduced. And there are no warn signs to replace.
These pumps are available in GRP-PP,PVDF for maximum chemical resistance. The lastest range has been created in SS-316-L,Hastelloy-C and Alloy-20
Daybreak' Magnetic drive chemical process pumps offer many benefits.
- Minimizes exposure of your personnel to hazardous chemicals.
- Eliminates contacting seal faces which are prone to wear and leakage.
- Provides superior corrosion resistance.
- Eliminates costly seal flush systems required on all pumps with double mechanical seals.
- Reduces downtime and maintenance costs through extended service intervals.
- Eliminates alignment problems inherent in direct-coupled units.
- They are ideal for vaccum service and transfer of expensive, toxic, radio active, hazardous and corrosive chemicals.
Application
Seal-less features make these pumps perfect for environments subject to federal regulations.
Chemical, Pharmaceutical, Textile Processing & Dye Baths Electroplating, Various Metal Rcovery Systems, Metal Finishing, Color Photo Procesing, T.V.Tube Processing, Food Processing: Dairies, Soft Drinks, Beverages, X-Ray Film, IC Photo Engraving Process/PCB Plants, Refrigeration & Chilling Plants,Water Treatment Plants, Galvanizing/Anodizing Plating Plants, Etching/Spark Erosion Machines & many more....where pump leakage must be avoided.