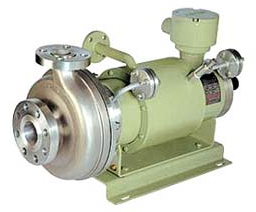
Type HT high temperature pumps are high temperature pumps suitable up to 400° C. These pumps differ in construction from basic pumps, as pump and motor are separated thermally by an adaptor which prevents heat transfer from the pump to motor area. In these pumps, an independent circulating system using same liquid being pumped with cooling jacket and heat exchanger is provided. The circulation is achieved with the aid of an auxiliary impeller mounted at the fore end of the motor chamber. The cooling arrangement permits the motor and bearings to operate at temperatures much lower than the processed fluid.
Fluids Handled
- Thermic fluid
- Vegetable oil
- High temperature hydrocarbons
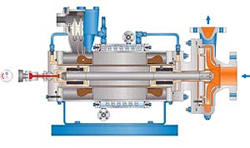
Specifications
- Flow : 1.0 m3/hr to 500 m3/hr
- Head : 150 m
- Temp : up to 400° C
- Pressure : 30 bar
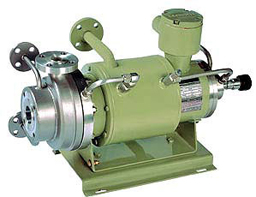
Type HM pumps for liquid with high melting point are high melting pumps for thermosensitive liquids with high solidifying temperature. These pumps are provided with a heating jacket on the outer body of the pump and motor to prevent liquid from solidifying during pump operation. Suited for fluids with melting points from ambient upto 150° C.
Specifications
- Flow : 1 to 500 m3/hr
- Head : upto 140m, higher head upon request
- Temp : up to 150° C
- Pressure : under full vacuum to 15 kg/cm2
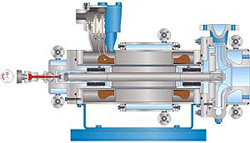
Applications
- Ideal for use in a wide range of services upto 150°C. Liquids with high melting points
- Resins
- Anhydrides (Malcic & Phthalic)
- Alkylated phenols etc. Fatty acid
- Acric Acid
- Glycerine
- Acetic Acid
- Ethylene Diamine
- Cresol
- Maleic Acid
- Heptane
- MDI (Methylene Diparaphenylene Isocyanate)
It is also ideal for services where heating and cooling is required to avoid liquid polymerization / crystallization.
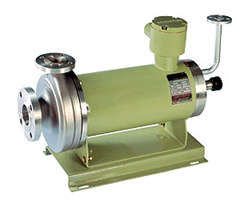
Type HR reverse circulation pumps are designed for fluids & chemicals with relatively high vapour pressure, low specific gravity, low specific heat liquids. Liquids with steep vapor pressure curves may vaporize on picking up the motor heat and result in cavitations conditions The circulation/pumping fluid is passed from the casing volute chamber into the rotor chamber through the front bearing housing. After being extracted from the outlet of rear bearing housing, the liquid is returned to vapor zone in the suction tank, through the reverse circulation line.
Specifications
- Flow : 1 to 500 m3/hr
- Head : upto 140m, higher head upon request
- Temp : -80 to 100° C
- Pressure : atmospheric to 15 kg/cm2
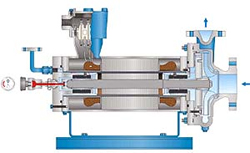
Applications
- Ammonia
- Freon and Refrigerants
- Anhydrous Hydrofluoric Acid
- Methylene Chloride
- Aceton
- Acetaldehyde
- Formaldehyde
- Vinyl Acetate
- Acrylonitril Etc.
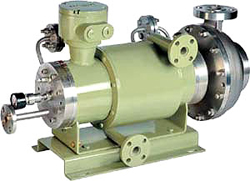
Type HS heavy duty slurry pumps are designed for slurry services. Clean liquid compatible to system liquid is flushed through the inlet port at the back of the motor to prevent the ingress of slurry into the motor area with back flushing line arrangement. The function of this arrangement is to prevent the slurry entering into the rotor chamber. This also lubricates the bearings. An auxiliary impeller located at fore end of the rotor circulates the flushing fluid through an integral heat exchanger to minimize frictional and electrical loss. The back flushing arrangement enables the pump to operate in process fluids with solid continent up to 5%.The back flush should be started at least one minute before switching on the pump and should be allowed to continue for a minute after shutting down the pump.

Operating Range
- Flow : 1 to 500 m3/hr
- Head : upto 140m, higher head upon request
- Temp : upto 150°C
- Pressure : atmospheric to 15 kg/cm2
Applications
- Ideal for use in light slurries with solids upto 5%
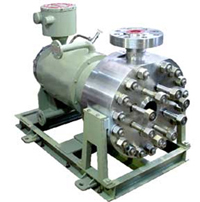
Hydrodyne offer specially designed vertical high pressure pumps for very high working pressures up to 450 bars. The pressure bearing parts are designed and manufactured as per AS ME section (iii) standard code.
Type HTHP High Temperature High Pressure Pumps also exhibit all the features and benefits of the standard canned motor pumps.